Specifications:
1. Plastic mould making & Injection moulding
2. Design assistance
3. High quality control and economic price
4. High-volume production
5. Continuance after-sale service support
Our product range:
1. Automobile mold & parts
2. Electricals mold & parts
3. Communications mold & parts
4. Household Appliance mold & parts
5. Deep barrel series mold & parts
6. Clear parts & mold
7. Precision parts & mold
Our main features:
1. CNC machines: 6 sets from 300-600 mm
2. Production capacity: 40 sets of molds per month
3. Molding trial machines size: 80-1300 tons
4. The resin we are familiar with: ABS, PC, POM, ABS+PC etc.
Mold Information for your reference:
1. Mould Base Standard : LKM Brand, Hasco, DME ect
2. Cavity/Core Material : NAK80, S136,8407,420,P20,718H,SKD61,FDAC ect
3. Hardness of the steel : 20-52HRC
4. Cavity Qty : Single-cavity / Multi-cavity
5. Runner : EVERTIP/MoldMax/ HASCO/ DME/ MOLD-MASTER Hot runner or Cold runner
6. Gate : Submarine gate, side/edge gate, direct gate ect
7. Plastic Part Materials: POM, ABS,PC, PC+ABS, PP, PMMA etc
8. Mould Life Time : 500,000-1,000,000 shots as per customers' requirement
9. Quality : ISO9001:2008 Certificate
10. Lead Time : 25-30 workdays based on the different products
11. Package : As per Customers' Requirement
12. Price Terms : FOB Waigaoqiao Port, China
13. Payment term: T/T
14. 48 Years Professional Manufacture Experience, Specialize in design and manufacture of Plastic Injection Mould and tooling for Home appliances, Electrical, Commodity, Automotive, Electronic equipment, Medical Products and other.
15. OEM orders are welcome.
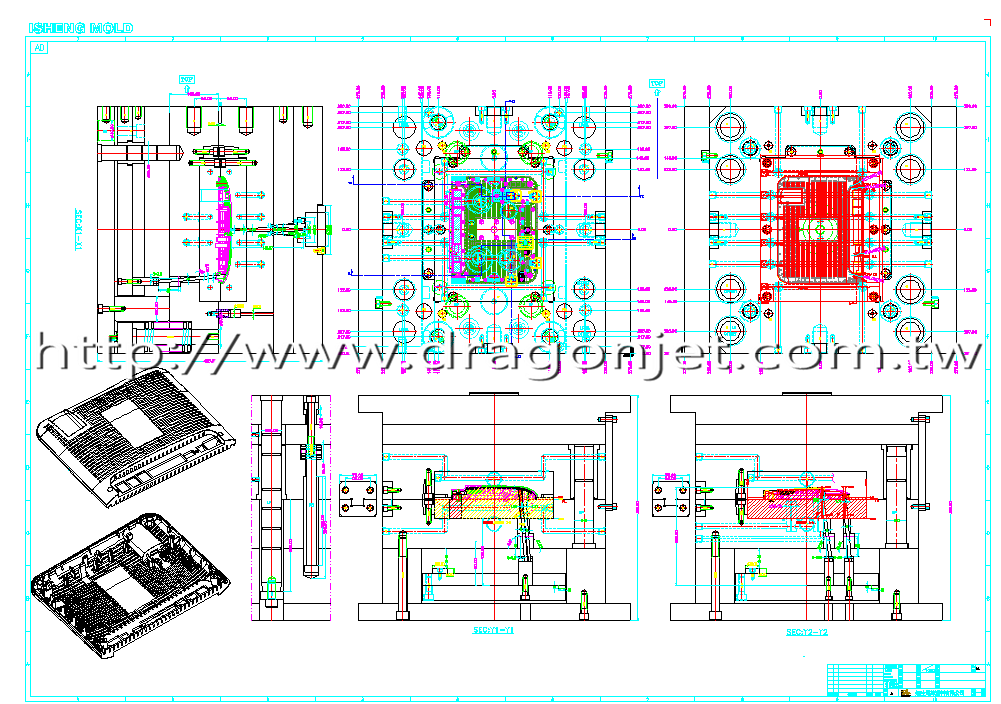
Our trade flow
1. Enquire /Quote: To offer us samples or drawings with any other requirements.
2. Negotiate Quality; Technique requests; Mould material; Price; Delivery time; Payment and so on.
3. Tooling Design:
New Tooling |
Tooling Fabrication Notice Related Specification Documents Tooling Assembly Drawing Mold Specification Review Sheet Review Tooling Structure and key areas of After-Tooling Processes with Bench-Work Dept., Engineering, and Molding Dept. Tooling Assembly & Drawing Modification Material Preparation 3D, 2D Tooling Component Drawings Verify 3D, 2D Drawings Convert 3D into IGS CAM Design Drawing to Tooling Production Personnel |
Tooling Design Change (ECN) |
Tooling Design Change (ECN) Notice Confirm difference between old and new drawing versions, and analyze design change feasibility. Review with Customer Review Tooling Modification Method Modified Tooling Drawing (Indicate Date) Convert 3D into IGS CAM Design (Arrange Schedule + No.) Issue Drawing to Tooling Production Personnel (Designers will classify old drawings as "void") |
Tooling Repair |
Tooling Repair Notice Confirm difference between tooling drawing and tooling abnormality Confirm difference between part drawing and part abnormality Tooling Repair Drawing 3D, 2D Tooling Component Drawings Convert 3D into STP CAM Design (Arrange Schedule + No.) Issue Drawing to Tooling Production Personnel (Designers will classify old drawings as "void") |
5. Mould Test: We will sent the sample's inspection report & injection parameters to the customer and inform them about the testing date.
6. Trial run, Pilot run and Mass production based on FO or PO. We have excellent equipment, short delivery time, efficient team, high quality control and perfect after-sale services.
7. Delivery according to customer requirements.
If you are interested in any of our products, please feel free to contact us. Also, you can know more about us from www. dragonjet.com.tw.
We sincerely want to establish long-term business relationship with you! We offer all kind of plastic products according to your drawing and requirements.
Specifications:
1. Plastic mould making & Injection moulding
2. Design assistance
3. High quality control and economic price
4. High-volume production
5. Continuance after-sale service support
Our product range:
1. Automobile mold & parts
2. Electricals mold & parts
3. Communications mold & parts
4. Household Appliance mold & parts
5. Deep barrel series mold & parts
6. Clear parts & mold
7. Precision parts & mold
Our main features:
1. CNC machines: 6 sets from 300-600 mm
2. Production capacity: 40 sets of molds per month
3. Molding trial machines size: 80-1300 tons
4. The resin we are familiar with: ABS, PC, POM, ABS+PC etc.
Mold Information for your reference:
1. Mould Base Standard : LKM Brand, Hasco, DME ect
2. Cavity/Core Material : NAK80, S136,8407,420,P20,718H,SKD61,FDAC ect
3. Hardness of the steel : 20-52HRC
4. Cavity Qty : Single-cavity / Multi-cavity
5. Runner : EVERTIP/MoldMax/ HASCO/ DME/ MOLD-MASTER Hot runner or Cold runner
6. Gate : Submarine gate, side/edge gate, direct gate ect
7. Plastic Part Materials: POM, ABS,PC, PC+ABS, PP, PMMA etc
8. Mould Life Time : 500,000-1,000,000 shots as per customers' requirement
9. Quality : ISO9001:2008 Certificate
10. Lead Time : 25-30 workdays based on the different products
11. Package : As per Customers' Requirement
12. Price Terms : FOB Waigaoqiao Port, China
13. Payment term: T/T
14. 48 Years Professional Manufacture Experience, Specialize in design and manufacture of Plastic Injection Mould and tooling for Home appliances, Electrical, Commodity, Automotive, Electronic equipment, Medical Products and other.
15. OEM orders are welcome.
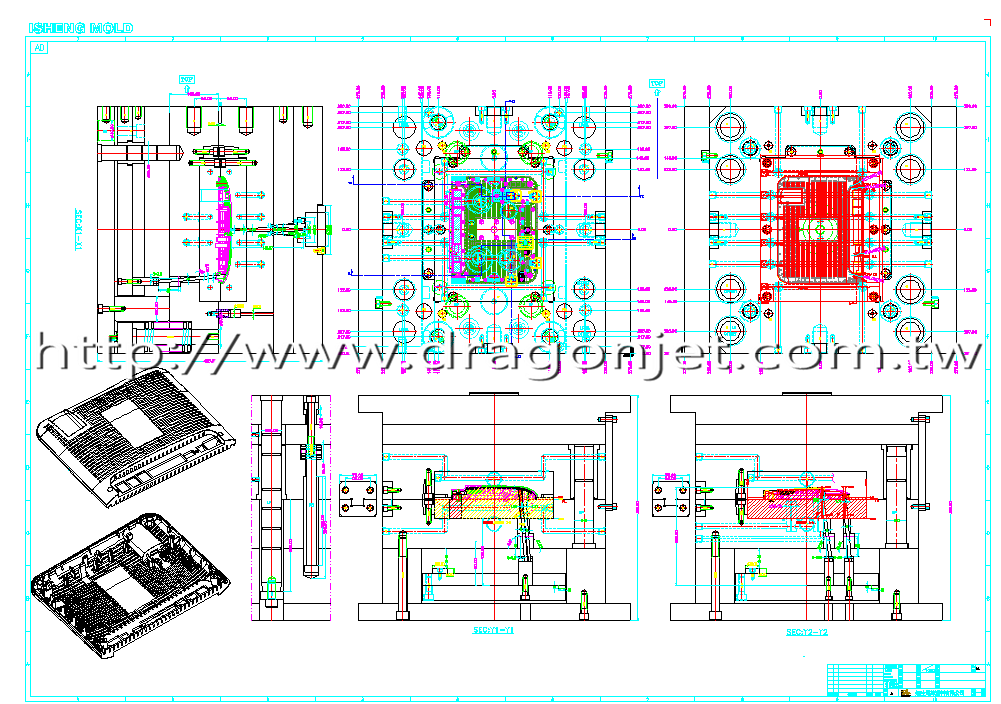
Our trade flow
1. Enquire /Quote: To offer us samples or drawings with any other requirements.
2. Negotiate Quality; Technique requests; Mould material; Price; Delivery time; Payment and so on.
3. Tooling Design:
New Tooling |
Tooling Fabrication Notice Related Specification Documents Tooling Assembly Drawing Mold Specification Review Sheet Review Tooling Structure and key areas of After-Tooling Processes with Bench-Work Dept., Engineering, and Molding Dept. Tooling Assembly & Drawing Modification Material Preparation 3D, 2D Tooling Component Drawings Verify 3D, 2D Drawings Convert 3D into IGS CAM Design Drawing to Tooling Production Personnel |
Tooling Design Change (ECN) |
Tooling Design Change (ECN) Notice Confirm difference between old and new drawing versions, and analyze design change feasibility. Review with Customer Review Tooling Modification Method Modified Tooling Drawing (Indicate Date) Convert 3D into IGS CAM Design (Arrange Schedule + No.) Issue Drawing to Tooling Production Personnel (Designers will classify old drawings as "void") |
Tooling Repair |
Tooling Repair Notice Confirm difference between tooling drawing and tooling abnormality Confirm difference between part drawing and part abnormality Tooling Repair Drawing 3D, 2D Tooling Component Drawings Convert 3D into STP CAM Design (Arrange Schedule + No.) Issue Drawing to Tooling Production Personnel (Designers will classify old drawings as "void") |
5. Mould Test: We will sent the sample's inspection report & injection parameters to the customer and inform them about the testing date.
6. Trial run, Pilot run and Mass production based on FO or PO. We have excellent equipment, short delivery time, efficient team, high quality control and perfect after-sale services.
7. Delivery according to customer requirements.
If you are interested in any of our products, please feel free to contact us. Also, you can know more about us from www. dragonjet.com.tw.
We sincerely want to establish long-term business relationship with you!
The boiler water wall is the main radiation heat surface, arranged inside the boiler chamber and proceeds the heat exchange directly with the high temperature flame. The convection tubes are the convection heat surface of the boiler, arranged between the boiler chamber outlet and the end heat surface and proceed the heat exchange directly with the high temperature fume. The water wall and convection tubes are the main heat surface of the boiler, the tubes diameter for both generally usedΦ 51-60mm boiler steel tubes, also as the request.
The first type is the bare pipe water wall. This is the simplest structure of the water wall. The advantage is that ordinary seamless steel pipes can be used, and it is more convenient to replace the water wall pipe. The disadvantage is that the temperature of the furnace wall is still high, and heavy refractory bricks are required. The steel frame of the corresponding boiler should be strengthened. , The air leakage of the furnace wall is relatively large. Old-fashioned high-pressure boilers and medium and small boilers are used more frequently.
The second tupe is the membrane water wall. The membrane water wall is welded by seamless steel tubes with fins. The Water Wall Tubes are connected by fins to make the water wall into a whole. This kind of water wall is called a membrane water wall. Its function is to strengthen the heat transfer of the water wall and greatly reduce the temperature of the furnace wall. The furnace wall does not need refractory bricks, but only requires thermal insulation materials. Compared with the conventional heavy furnace wall, the weight can be reduced by 60% ~ 70%, the furnace wall heat storage is reduced by 80%, the start and stop time is shortened, and the fuel consumption is reduced. The load of the furnace steel frame is greatly reduced, saving refractory materials and steel.
The third type is the pierced pipe water wall. The barbed pipe water wall pipe is made by welding many grab nails with a length of 20 to 26 mm and a diameter of 6 to 12 mm on the water wall pipe. It is mainly used to lay the gas belt. Generally, for boilers that burn fuel with low calorific value and low volatile content, in order to stabilize the fire, pierced pipe water walls are often used for laying the fire protection belt.
Wall Mounted Boiler,Water Wall Tubes,Wall Mounted Combi Boiler,Water Wall Tubes In Boiler
Jinan Yuanda Power Equipment Co.,Ltd. , https://www.ydboilerpart.com