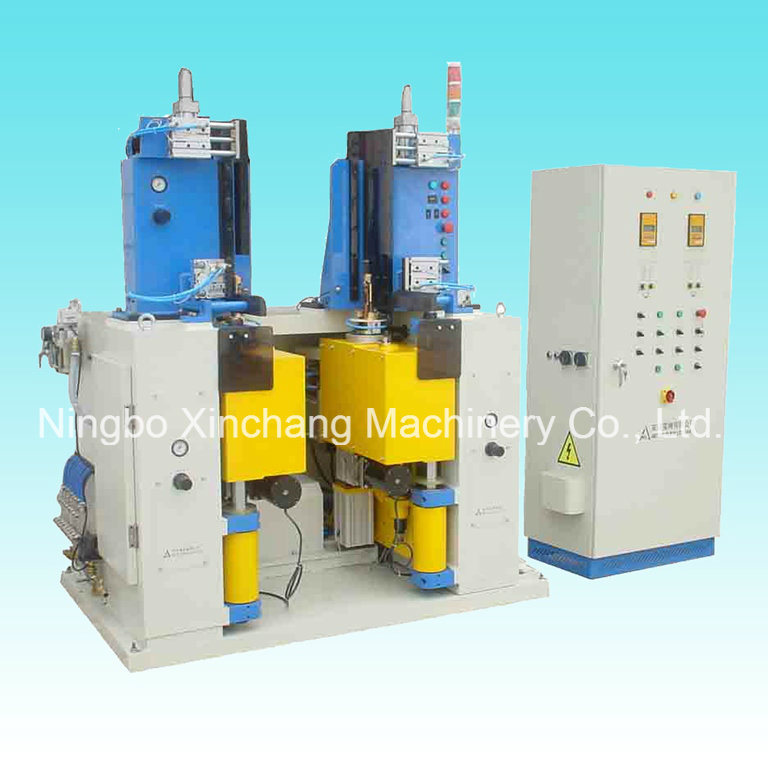
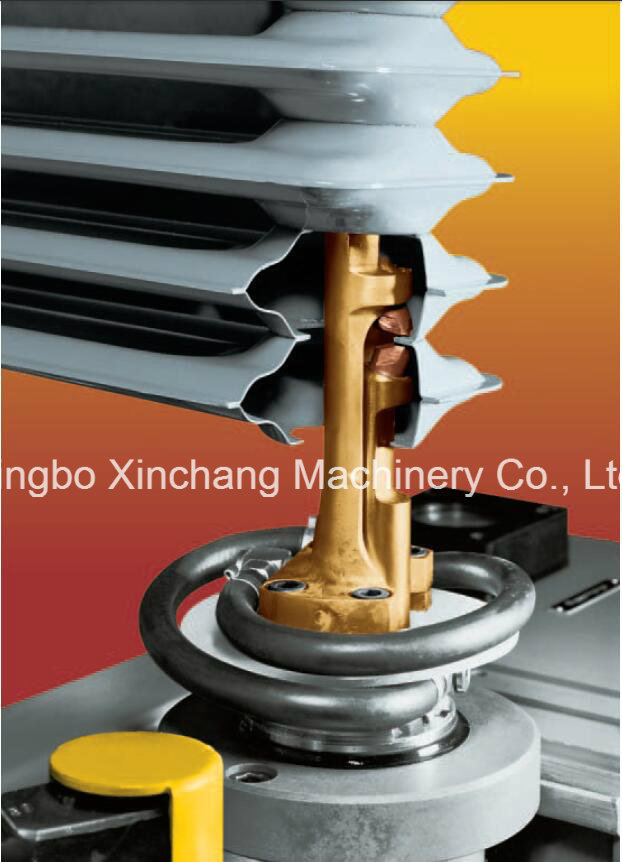
 Main Functions
The automatic circumferential spot welding machine(Radiator boss stitch welding machine) is one resistance welding equipment for the boss between the Oil filled heater, It is featured with reliable welding, good sealing, high efficiency, low cost, etc. The mainframe comprises the touch screen, PLC control, silicon controlled rectifier (SCR) as the phase switch, with the high-performance components, the stable welding quality, and the overheating, air pressure, water flow and other protection warning functions.
Process Parameters
The pass rate of oil heater after welding≥95% (Calculated by sets).
Main Parameters of Equipment
1 | Basic Parameters | |||
1.1 | Convex hole distance | 225-490mm (adjustable) | ||
1.2 | Convex hole diameter | Φ42-Φ44mm | ||
1.3 | Length of Oil filled heater | 325-600mm (regulated according to the workpiece) | ||
1.4 | Width of Oil filled heater | 100-180mm (regulated according to the workpiece) | ||
1.5 | Max. number of elements per set of radiator | 15 | ||
1.6 | Thickness of weldable sheet | 0.4-0.8mm (Ust1203 grade cold-drawn steel sheet) | ||
1.7 | Rated voltage | 380V/50Hz | ||
1.8 | Rated capacity | 50 × 2 (in the intermediate inverter, energy-saving, stable) | ||
1.9 | Duty cycle (%) | 50 | ||
1.10 | Secondary no-load voltage (V) | 9.4 | ||
1.11 | Secondary max. welding current (KA): | ≥16 | ||
1.12 | Total resistance of secondary circuit (μΩ) | ≤50 | ||
1.13 | Weldment dimensions |
A=D+2*(55-90) (mm); D: 460-480 (mm)(Normal; E: 55-90 (mm) ; B: 100-200 (mm) G: 6(Tl20 (mm); C: 40-45 (mm); F: OC+12 (ram); H: 38-42 (mm) |
||
2 | Overall Requirements | |||
2.1 | Wire size | ≥35mm2 | ||
2.2 | Number of circumferential convex hole welding spots | 32-41 | ||
2.3 | Max. welding speed (S) excluding other auxiliary time: | ≤16 seconds/PC (calculated y 38 spots per ring, with reference to 0.5mm low-carbon cold-rolled sheets, steel material complies with EN10130 stamping steel sheet U St grade (or no less than GB/T222 standard, carbon content: 0.05-0.12%) | ||
2.4 | Acceptance standards of welding machine: | Comply with the general standards of PRC and the GB15578-1995 national mandatory certification standards. And manufactured in line with the applicable standards, e.g.: JB/T3158-1999, JB3957-1999. | ||
2.5 | Controller: | PLC + Touch screen Chinese UI, the controller uses a microprocessor (closed-loop control), current slowly rising, welding spots recorded and number of welding set, 8 sets of welding parameters stored, execution directly selected, with security lock for the setting of welding parameters, startup self-test and system failure self-test, overheating protection and fault indication, etc. Equipped with the master switch and emergency stop button. | ||
2.6 | Auxiliary time including each component feeding | About 2-5S (according to different operators) | ||
2.7 | Flow of cooling water | ≥30L/min (added with the water flow detection warning system) | ||
Temperature of cooling water | At the water inlet≤30ºC | |||
Pressure of cooling water (Mpa) | 0.15-0.3 | |||
2.8 | Compressed air (Mpa) | 0.5-0.6 (added with the pressure detection warning system at the compressed air input) | ||
2.9 | Max. electrode pressure (N) (0.6Mpa): | ≥3,000 | ||
2.10 | Mainframe weight | 1,800Kg | ||
2.11 | Repair tools | 1 set per 3 units | ||
2.12 | Provided with Mitsubishi touch screen and Mitsubishi PLC, Japan SMC solenoid valve and cylinder assembly, Omron auxiliary relay, Siemens converter; | |||
2.13 | Hands-on button control using the mobile station. | |||
3 | Configurations | |||
NO. | Name | Brand/Place of Origin | Remark | |
3.1 | Solenoid valve | SMC | Â | |
3.2 | Regulating valve/Filter assembly/Pressure Gauge | MindMan | Â | |
3.3 | Air connector/Flow limit valve | SMC | Â | |
3.4 | Master cylinder, 2 sets | Imported components, Japan (World Famous Brand) | Assembled by ourself | |
3.5 | Welding controller system, 2 sets | Anda, independent development | The arm rotary cylinder part uses SMC components | |
3.6 | Main converter, 2 sets | Anda | Epoxy resin package | |
3.7 | Inverter, 2 sets | European imported elements | Designed and assembled by Anda | |
3.8 | Touch screen, 1 set | Mitsubishi | Â | |
3.9 | PLC/Touch screen | Mitsubishi | Â | |
3.10 | SCR/ Diode/IGBT | Ximenkan or equivalent foreign brands | Â | |
3.11 | Auxiliary relay | Omron or equivalent foreign brands | Â | |
3.12 | Proximity switch | Autonics | Â | |
3.13 | Button switch | Siemens/ Schneider | Â | |
3.14 | Power switch | Mitsubishi/Japan | Â | |
3.15 | Stepping motor, 2 sets | Sanyo/Japan | Â | |
3.16 | Driver, 2 sets | Domestic | Â | |
3.17 | Time relay | Omron | Â | |
3.18 | Bearing | Wholly Imported, Famous Brand | Â |
Â
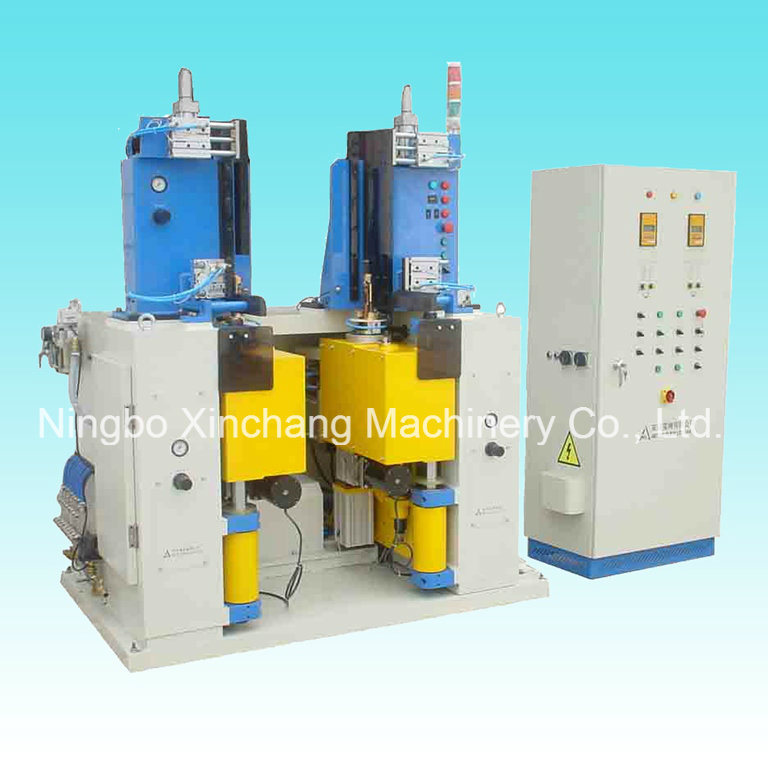
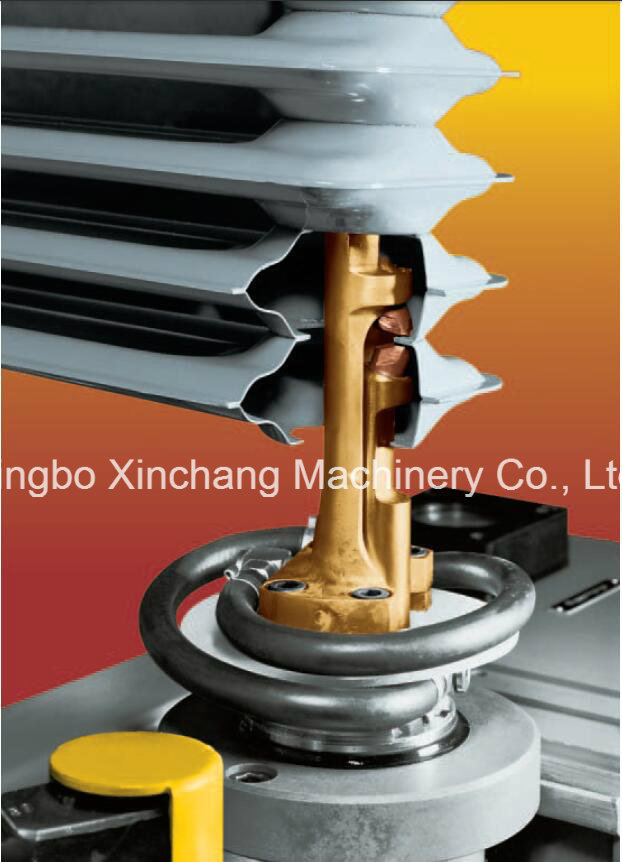
 Main Functions
The automatic circumferential spot welding machine(Radiator boss stitch welding machine) is one resistance welding equipment for the boss between the Oil filled heater, It is featured with reliable welding, good sealing, high efficiency, low cost, etc. The mainframe comprises the touch screen, PLC control, silicon controlled rectifier (SCR) as the phase switch, with the high-performance components, the stable welding quality, and the overheating, air pressure, water flow and other protection warning functions.
Process Parameters
The pass rate of oil heater after welding≥95% (Calculated by sets).
Main Parameters of Equipment
1 | Basic Parameters | |||
1.1 | Convex hole distance | 225-490mm (adjustable) | ||
1.2 | Convex hole diameter | Φ42-Φ44mm | ||
1.3 | Length of Oil filled heater | 325-600mm (regulated according to the workpiece) | ||
1.4 | Width of Oil filled heater | 100-180mm (regulated according to the workpiece) | ||
1.5 | Max. number of elements per set of radiator | 15 | ||
1.6 | Thickness of weldable sheet | 0.4-0.8mm (Ust1203 grade cold-drawn steel sheet) | ||
1.7 | Rated voltage | 380V/50Hz | ||
1.8 | Rated capacity | 50 × 2 (in the intermediate inverter, energy-saving, stable) | ||
1.9 | Duty cycle (%) | 50 | ||
1.10 | Secondary no-load voltage (V) | 9.4 | ||
1.11 | Secondary max. welding current (KA): | ≥16 | ||
1.12 | Total resistance of secondary circuit (μΩ) | ≤50 | ||
1.13 | Weldment dimensions |
A=D+2*(55-90) (mm); D: 460-480 (mm)(Normal; E: 55-90 (mm) ; B: 100-200 (mm) G: 6(Tl20 (mm); C: 40-45 (mm); F: OC+12 (ram); H: 38-42 (mm) |
||
2 | Overall Requirements | |||
2.1 | Wire size | ≥35mm2 | ||
2.2 | Number of circumferential convex hole welding spots | 32-41 | ||
2.3 | Max. welding speed (S) excluding other auxiliary time: | ≤16 seconds/PC (calculated y 38 spots per ring, with reference to 0.5mm low-carbon cold-rolled sheets, steel material complies with EN10130 stamping steel sheet U St grade (or no less than GB/T222 standard, carbon content: 0.05-0.12%) | ||
2.4 | Acceptance standards of welding machine: | Comply with the general standards of PRC and the GB15578-1995 national mandatory certification standards. And manufactured in line with the applicable standards, e.g.: JB/T3158-1999, JB3957-1999. | ||
2.5 | Controller: | PLC + Touch screen Chinese UI, the controller uses a microprocessor (closed-loop control), current slowly rising, welding spots recorded and number of welding set, 8 sets of welding parameters stored, execution directly selected, with security lock for the setting of welding parameters, startup self-test and system failure self-test, overheating protection and fault indication, etc. Equipped with the master switch and emergency stop button. | ||
2.6 | Auxiliary time including each component feeding | About 2-5S (according to different operators) | ||
2.7 | Flow of cooling water | ≥30L/min (added with the water flow detection warning system) | ||
Temperature of cooling water | At the water inlet≤30ºC | |||
Pressure of cooling water (Mpa) | 0.15-0.3 | |||
2.8 | Compressed air (Mpa) | 0.5-0.6 (added with the pressure detection warning system at the compressed air input) | ||
2.9 | Max. electrode pressure (N) (0.6Mpa): | ≥3,000 | ||
2.10 | Mainframe weight | 1,800Kg | ||
2.11 | Repair tools | 1 set per 3 units | ||
2.12 | Provided with Mitsubishi touch screen and Mitsubishi PLC, Japan SMC solenoid valve and cylinder assembly, Omron auxiliary relay, Siemens converter; | |||
2.13 | Hands-on button control using the mobile station. | |||
3 | Configurations | |||
NO. | Name | Brand/Place of Origin | Remark | |
3.1 | Solenoid valve | SMC | Â | |
3.2 | Regulating valve/Filter assembly/Pressure gauge | MindMan | Â | |
3.3 | Air connector/Flow limit valve | SMC | Â | |
3.4 | Master cylinder, 2 sets | Imported components, Japan (World Famous Brand) | Assembled by ourself | |
3.5 | Welding controller system, 2 sets | Anda, independent development | The arm rotary cylinder part uses SMC components | |
3.6 | Main converter, 2 sets | Anda | Epoxy resin package | |
3.7 | Inverter, 2 sets | European imported elements | Designed and assembled by Anda | |
3.8 | Touch screen, 1 set | Mitsubishi | Â | |
3.9 | PLC/Touch screen | Mitsubishi | Â | |
3.10 | SCR/ Diode/IGBT | Ximenkan or equivalent foreign brands | Â | |
3.11 | Auxiliary relay | Omron or equivalent foreign brands | Â | |
3.12 | Proximity switch | Autonics | Â | |
3.13 | Button switch | Siemens/ Schneider | Â | |
3.14 | Power switch | Mitsubishi/Japan | Â | |
3.15 | Stepping motor, 2 sets | Sanyo/Japan | Â | |
3.16 | Driver, 2 sets | Domestic | Â | |
3.17 | Time relay | Omron | Â | |
3.18 | Bearing | Wholly Imported, Famous Brand | Â |
Â
If your weld isn't on a piece of metal that will show, or if you don't care about how the weld looks, then you are done with your weld. However, if the weld is showing or you are welding something that you want to look nice then you will most likely want to grind down your weld and smooth it out.
Slap a grinding wheel onto an angle grinder and get started grinding on the weld. The neater your weld was the less grinding you will have to do, and after you have spent a whole day grinding, you will see why it's worth it to keep your welds neat in the first place. If you use a ton of wire and made a mess of things it's ok, it just means that you might be grinding for a while. If you had a neat simple weld though, then it shouldn't take too long to clean things up.
Be careful as you approach the surface of the original stock. You don't want to grind through your nice new weld or gouge out a piece of the metal. Move the angle grinder around like you would a sander so as not to heat up, or grind away any one spot of the metal too much. If you see the metal get a blue tinge to it you are either pushing too hard with the grinder or not moving the grinding wheel around enough. This is can happen especially easily while grinding thing sheets of metal.
Grinding welds can take a while to do depending on how much you have welded and can be a tedious process - take breaks while grinding and stay hydrated. (Grinding rooms in shops or studios tend to heat up, especially if you are wearing leathers). Wear a full face mask when grinding, a mask or respirator, and ear protection. Make sure that all your clothing is neatly tucked in and that you don't have anything hanging down from your body that could get caught in the grinder - it spins fast and it can suck you in!
When you are done your piece of metal might look something like the one in the second photo pictured below. (Or maybe better as this was done by a few Instructables Interns at the beginning of the summer during their first welding experience.)
Step 8: Common Problems
Welding Grinding,Tig Welding Helmet,Welding Grinding Helmet,Metal Welding Grinding
Changzhou Edaweld Trading Company Limited , https://www.edaweld.com