I. Introduction to Laser Cutting Machine Wattage
Laser cutting technology has revolutionized the manufacturing and fabrication industries. It offers unparalleled precision, speed, and versatility. At the heart of this technology lies the laser cutting machine's wattage, a critical factor that can significantly influence cutting performance, efficiency, and the range of materials that can be processed.
Understanding the importance of laser cutting machine wattage is essential for optimizing production processes and achieving desired outcomes in various applications.
Definition of Laser Cutting Power
Laser cutting power refers to the amount of energy delivered by the laser to the material being cut, typically measured in watts (W). It represents the power output of the laser equipment and directly relates to the intensity of the laser beam.
Importance of Laser Cutting Machine Wattage
The wattage of a laser cutting machine determines the power output of the laser beam, directly impacting its cutting capabilities. Higher-wattage lasers can cut through thicker and denser materials more quickly and with greater precision, while lower-wattage lasers are typically used for finer, more detailed work on thinner materials.
Selecting the appropriate wattage for a specific application is crucial for achieving optimal results, minimizing material waste, and ensuring operational efficiency.
II. Types of Laser Cutting Machines
Laser cutting technology encompasses various types of machines, each utilizing different laser sources and suited to specific applications. Understanding the distinctions between these machines is fundamental for selecting the appropriate equipment for your cutting needs.
Criteria | Fiber Laser | CO2 Laser | YAG Laser |
Power Range (W) | 500 - 40,000 | 30 - 4,000 | 50 - 1,000 |
Wavelength | 1.064 or 1.55 microns | 10.6 microns | 1.064 microns |
Materials | Metals, coated metals, some plastics | Organic materials (wood, acrylic, plastics, fabrics, glass) | Metals, ceramics, composites |
Advantages | - High efficiency - Low maintenance - Long lifespan - Compact size - Excellent beam quality - Fast cutting speeds | - Versatile for non-metals - Good for thick materials - Lower initial cost - Suitable for large-scale cutting | - Strong power output - Exceptional beam quality - Flexibility in operating modes - Wide range of materials - Suitable for medical applications |
Typical Applications | - Metal cutting and welding - Marking and engraving - Industrial manufacturing - Microelectronics | - Cutting non-metals - Engraving - Packaging industry - Textile cutting | - Cutting and welding thick materials - Medical (ophthalmology, dermatology) - Scientific research - Automotive industry |
III. How Wattage Affects Laser Cutting Performance
Laser cutting is a precise method used in various industries to cut materials with high accuracy and efficiency. The wattage of a laser cutting machine plays a crucial role in determining its effectiveness.
It influences key aspects of the cutting process, including cutting speed, material thickness, and edge quality. Understanding how wattage impacts these factors is essential for optimizing cutting operations and achieving the desired outcomes.
Cutting Speed and Precision
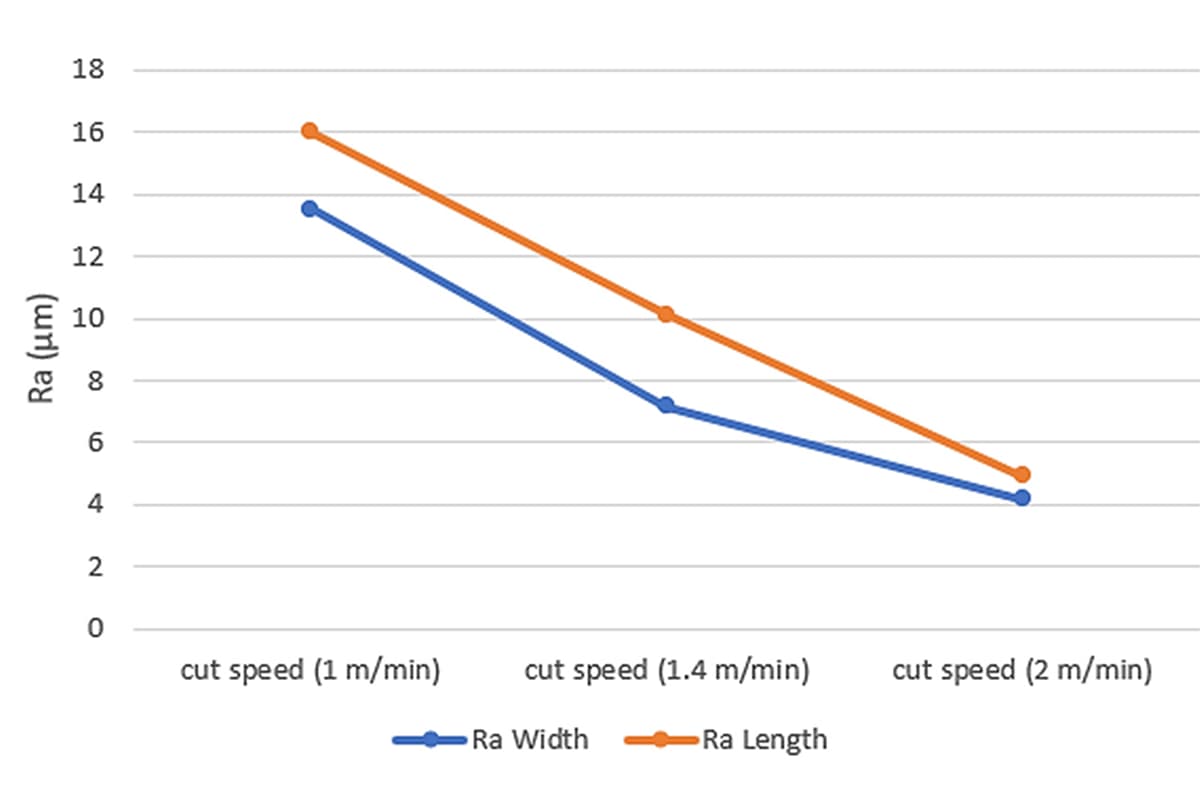
Cutting Speed
One of the most direct impacts of laser wattage is on cutting speed. Higher wattage lasers generate more powerful beams, allowing them to cut through materials faster compared to lower wattage lasers. This increased speed translates to higher productivity and shorter cycle times, making high-wattage lasers suitable for high-volume production environments.
For instance, a fiber laser cutting machine cuts 1mm thick steel: A 1000W laser can cut at speeds of 10.0-13.2 m/min. A 2000W laser can cut at speeds of 25.0-31.0 m/min. The higher power allows the laser to melt and vaporize the material more efficiently, resulting in quicker cuts. In contrast, a lower wattage laser would take longer to achieve the same result, potentially leading to bottlenecks in the production process.
Precision
Achieving high precision requires careful calibration of wattage, especially for intricate designs and fine detailing. Lower-wattage lasers are often preferred for such tasks to maintain control over the thermal impact on the material.
Speed vs. Precision
There is often a trade-off between speed and precision. Higher wattage allows for faster cuts but may compromise the detail and accuracy required for intricate work. Conversely, lower wattage provides finer control but at the expense of cutting speed.
Material Type and Thickness
Material Thickness
The ability to cut through different material thicknesses is another area where wattage plays a crucial role. Higher wattage lasers are capable of cutting through thicker and denser materials with ease. This capability expands the range of materials that can be processed, allowing manufacturers to tackle more demanding projects.
The increased power of higher wattage lasers ensures that the beam can penetrate deeper into the material, maintaining a high-quality cut even at greater thicknesses.
Material Type
- Metals: Cutting metals like steel, aluminum, or titanium demands higher wattage due to their density and heat resistance. Metals require sufficient power to generate the necessary thermal energy to melt and vaporize the material.
- Plastics: Plastics generally require lower wattage compared to metals, but the specific type of plastic can impact the necessary power levels. Thermoplastic materials (e.g., acrylic) often need more precise control to avoid melting or warping.
- Organic Materials: Wood, leather, and textiles are more easily cut with lower wattage lasers. These materials are more susceptible to charring and burn marks, so precise control over power output is essential.
Desired Cut Quality
The wattage of a laser cutting machine directly influences the quality of the cut, including aspects like edge smoothness, burr formation, and heat-affected zones.
Edge Smoothness
- Higher Wattage: Machines with higher wattage can produce smoother edges on thick or dense materials by providing consistent power, reducing the likelihood of jagged edges.
- Lower Wattage: For thinner materials, lower wattage machines can achieve smooth edges without excessive thermal distortion.
Burr Formation
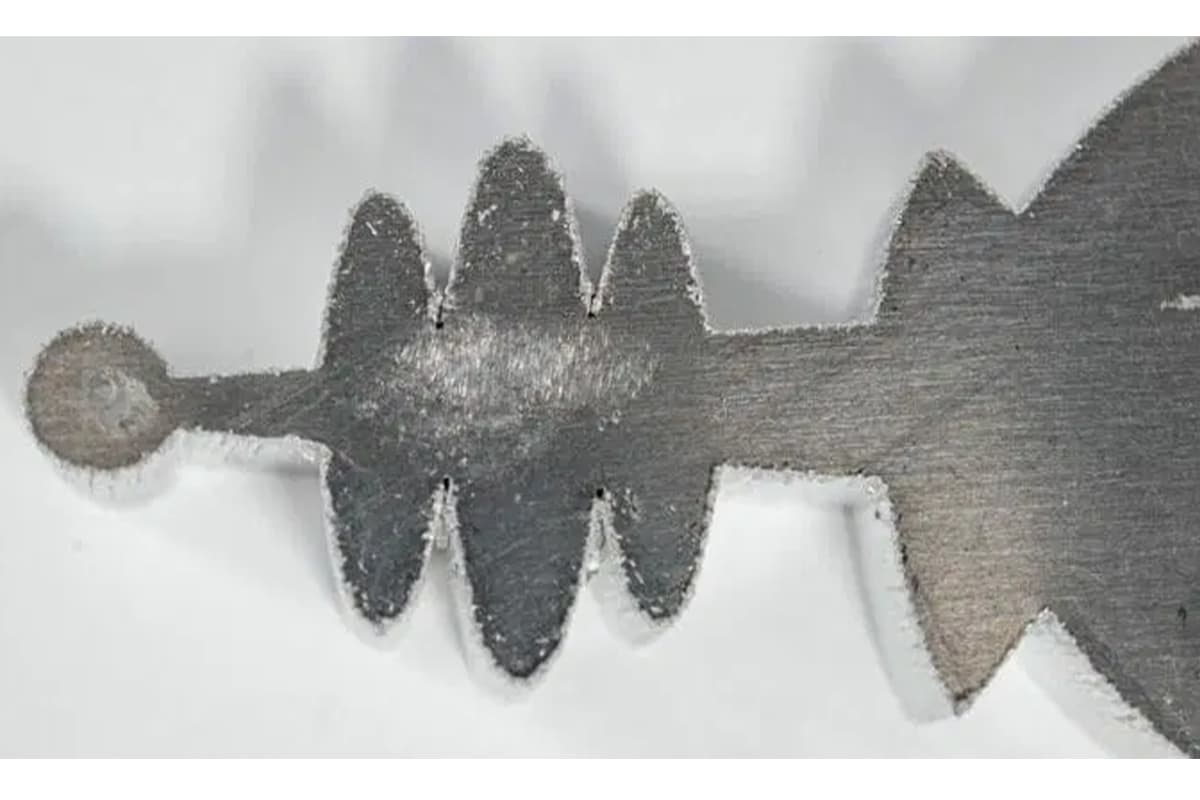
- Reduction of Burrs: Higher wattage allows for cleaner cuts with fewer burrs, reducing the need for secondary processing. This is particularly critical for metal cutting, where post-process deburring can be time-consuming and costly.
- Controlled Power: Lower wattage machines excel in tasks that require minimal burr formation on delicate materials like plastics and thin metals.
Heat-Affected Zones
Minimizing Thermal Impact: Managing heat-affected zones is crucial for maintaining material integrity. Lower wattage machines are effective for delicate materials, whereas higher wattage machines, with proper cooling and speed settings, can minimize thermal impact on thicker materials.
IV. Laser Cutting Machine Wattage Categories
Low Wattage Machines
Low wattage laser cutting machines typically range from 10 watts to 100 watts. These machines are ideal for applications that require delicate and precise work on thinner materials. Common materials processed with low wattage lasers include paper, textiles, thin plastics, and certain types of wood.
Advantages of Low Wattage Machines:
- Precision and Fine Detail: Low wattage machines excel in achieving fine detail while engraving, making them suitable for intricate designs and patterns.
- Cost-Effective: Generally, these machines are more affordable and consume less power, making them economically attractive for small businesses and hobbyists.
- Safety: Lower power levels reduce the risk of material damage and are easier to handle, translating to safer operation conditions.
Limitations of Low Wattage Machines:
- Limited Material Thickness: These machines are not suitable for cutting thick or dense materials due to insufficient penetrative power.
- Slower Cutting Speeds: Compared to higher wattage machines, the cutting process is slower, potentially affecting productivity.
- Limited Versatility: Specific applications may fall beyond the capabilities of low wattage machines, necessitating alternatives for certain tasks.
Medium Wattage Machines
Medium wattage laser cutting machines generally have power levels ranging from 100 watts to 500 watts. These machines strike a balance between versatility and operational cost, suitable for a broad spectrum of materials such as metals, thicker plastics, and composite materials.
Advantages of Medium Wattage Machines:
- Versatility: Capable of handling a wider range of materials and tasks, these machines are well-suited for diverse industrial applications.
- Balanced Speed and Precision: Adequate power allows reasonably fast cutting speeds while maintaining precision, balancing both productivity and quality.
- Economical: They offer a middle-ground solution, providing enhanced capabilities without the higher costs associated with high wattage machines.
Limitations of Medium Wattage Machines:
- Moderate Thickness Limitations: While more powerful than low wattage machines, medium wattage lasers may still struggle with extremely thick or tough materials.
- Higher Operational Costs: As wattage increases, so does power consumption and the associated operating costs.
- Complexity in Setup: These machines may require more sophisticated setup and maintenance protocols compared to their lower wattage counterparts.
High Wattage Machines
High wattage laser cutting machines typically operate within the range of 500 watts to 2000 watts. These machines are designed to tackle challenging tasks involving thick or dense materials, such as metals, stone, and high-performance composites.
Advantages of High Wattage Machines:
- High Capabilities: Exceptional cutting power allows for processing thicker and tougher materials with ease.
- Enhanced Productivity: Higher wattage equates to faster cutting speeds, significantly improving throughput in industrial environments.
- Superior Quality: The increased power often leads to cleaner cuts with minimal post-processing, enhancing product quality.
Limitations of High Wattage Machines:
- Higher Cost: Initial investment, as well as operational costs, are considerably higher due to the energy requirements and complexity of the machinery.
- Safety Concerns: Operating high wattage machines entails greater safety risks, requiring stringent safety protocols and trained personnel.
- Energy Consumption: These machines consume more power, impacting operational efficiency and environmental sustainability.
Industrial-grade Wattage Machines
Industrial-grade wattage laser cutting machines generally exceed 2000 watts, capable of reaching beyond 10,000 watts. These machines are used for heavy-duty applications in industries such as automotive, aerospace, and shipbuilding.
Advantages of Industrial-grade Wattage Machines:
- Unmatched Cutting Power: These machines can cut through extremely thick and dense materials with unparalleled ease and precision.
- Maximum Efficiency: Exceptionally high cutting speeds enhance productivity, making them suitable for high-volume production settings.
- Robust Construction: Built to withstand rigorous industrial environments, offering durability and longevity.
Limitations of Industrial-grade Wattage Machines:
- Environmental Impact: High power consumption and associated emissions make it crucial to implement mitigating measures to adhere to environmental regulations.
- Exorbitant Costs: The acquisition, maintenance, and operational costs can be prohibitively high, warranting substantial financial investment.
- Complexity and Maintenance: These machines demand extensive setup, calibration, and continuous maintenance to operate effectively.
V. Selecting the Right Wattage for Different Materials
This section explores the recommended wattages for various materials, including metals, plastics, wood, and fabrics. Understanding these recommendations will help in optimizing your laser cutting processes and ensuring superior results.
Metals
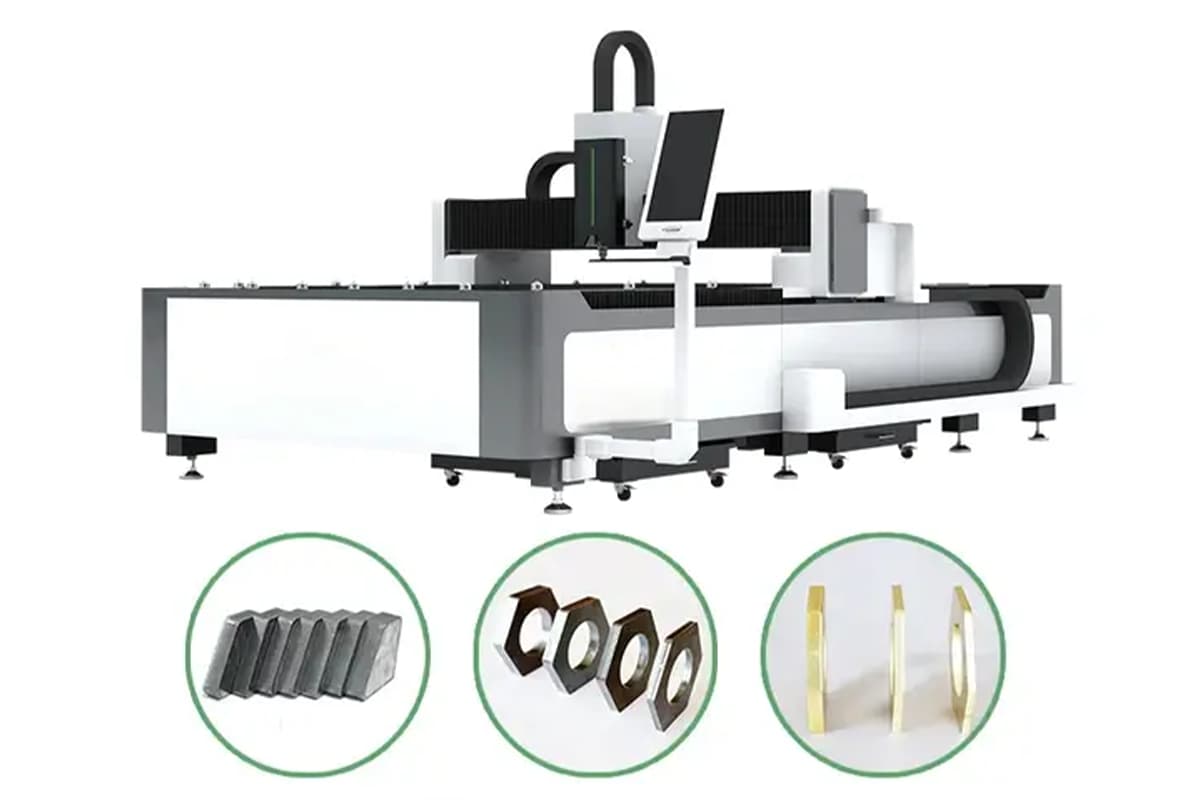
Metals are among the most common materials processed using laser cutting. Due to their density and thermal conductivity, metals require higher wattage lasers to achieve clean cuts.
Steel
- Thin Sheets (up to 1/8 inch): 500-750 watts
- Thicker Plates (up to 0.39 inches or more): 1000-2000 watts
- Example: A 2000-watt laser cutter can efficiently cut through a 20mm (about 0.79 inches) thick steel plate used in automotive manufacturing.
Aluminum
- Thin Sheets: 750-1000 watts
- Thicker Plates: 1000-2000 watts
- Note: Aluminum's reflective properties necessitate the use of fiber or disk lasers to prevent beam reflection and potential damage to the machine.
Copper and Brass
- Range: 500-3000 watts, depending on thickness
- Note: Higher wattages are often required due to high reflectivity and thermal conductivity.
Plastics
Plastics are more sensitive to heat, so lower wattages are generally used to avoid melting or burning the material.
Acrylic
- General Range: 60-150 watts
- Thickness: Suitable for sheets up to 1/2 inch thick
- Note: Lower wattages ensure smooth edges and prevent excessive melting.
Polycarbonate
- Thin Sheets: 100-200 watts
- Thicker Materials: May require higher wattages with careful control of cutting speed and cooling
- Note: Polycarbonate tends to discolor and melt, so precise control is essential.
Wood
Wood is widely used in laser cutting for applications ranging from furniture to decorative items. The appropriate wattage depends on the type of wood and its thickness.
Softwoods
- General Range: 40-100 watts
- Thickness: Up to 1/4 inch
- Note: Higher wattages may be needed for thicker pieces to ensure clean cuts without charring.
Hardwoods
- General Range: 100-200 watts
- Thickness: Up to 1/2 inch
- Thicker Hardwoods: 400 watts may be necessary
- Note: Hardwoods like oak and maple require more power due to their density.
Fabrics
Fabrics are delicate and require careful handling to avoid burning or fraying. Lower wattages are generally preferred to maintain the integrity of the material.
Natural Fabrics
- Range: 30-100 watts
- Materials: Cotton, wool, silk
- Note: These wattages are sufficient to cut through the fabric without causing excessive heat damage.
Synthetic Fabrics
- Range: 50-150 watts
- Materials: Polyester, nylon
- Note: Use the minimum power necessary to achieve a clean cut, reducing the risk of melting or burning.
Practical Considerations
When selecting the right wattage for different materials, consider the following practical tips:
- Material Testing: Conduct test cuts on sample materials to determine the optimal wattage and cutting parameters for your specific application.
- Beam Focus: Ensure proper beam focus for precise cuts. Adjust the focal length of the laser lens based on the material thickness.
- Cooling and Ventilation: Proper cooling and ventilation systems help manage heat generated during cutting, especially for thicker and more heat-sensitive materials.
VI. Wattage and Laser Cutting Applications
Industrial Manufacturing
Industrial manufacturing is one of the primary sectors that benefit from laser cutting technology. High wattage lasers are particularly advantageous in this industry due to the need for rapid and precise cutting of robust materials.
Automotive Industry
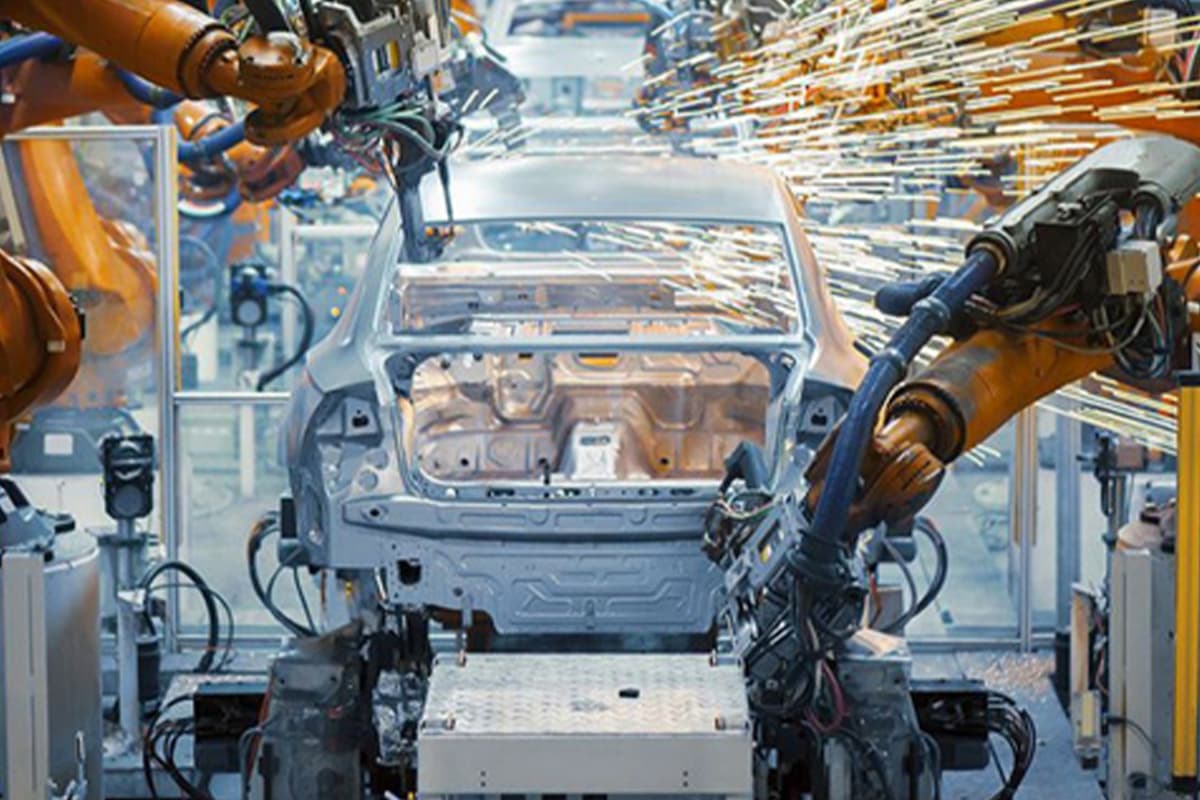
- Typical Wattage: 1000-3000 watts
- Applications: Cutting and welding car body components, exhaust systems, and other metal parts.
- Benefits: High wattage lasers provide the speed and precision needed for efficient mass production and strict tolerances. By significantly reducing cutting times, high wattage lasers help manufacturers lower production costs and increase output efficiency. This technology also enhances product quality by ensuring consistent and clean cuts, which is essential for the durability and safety of automotive parts.
Aerospace Industry
- Typical Wattage: 2000-6000 watts
- Applications: Cutting high-strength alloys and composite materials used in aircraft and spacecraft manufacturing.
- Benefits: The ability to cut through thick and dense materials with high precision maintains the structural integrity required in aerospace applications. Laser cutting's precision ensures compliance with strict aerospace safety standards, reducing the risk of material failure during flight. This technology also supports the production of complex geometries that are often necessary in aerospace design.
Art and Design
The art and design sector often utilizes laser cutting for creating intricate patterns and detailed pieces. Lower wattage lasers are typically sufficient for these applications, especially when working with thinner, more delicate materials.
Decorative Arts
- Typical Wattage: 50-150 watts
- Applications: Cutting and engraving on materials such as paper, wood, acrylic, and fabric.
- Benefits: Enables artists to achieve fine details and complex designs with smooth edges, enhancing the aesthetic quality of the finished pieces.
Jewelry Making
- Typical Wattage: 100-200 watts
- Applications: Cutting and engraving precious metals and gemstones.
- Benefits: Provides high precision and control, allowing for the creation of intricate and delicate jewelry pieces. This precision not only enhances the beauty of the designs but also ensures the durability and wearability of the jewelry.
Medical Uses
The medical industry relies on laser cutting technology for the production of medical devices and instruments. The required wattage varies based on the material and complexity of the components being manufactured.
Medical Device Manufacturing
- Typical Wattage: 150-500 watts
- Applications: Cutting and shaping medical-grade metals and plastics for devices such as stents, surgical tools, and implants.
- Benefits: High precision and clean cuts are essential for ensuring the safety and functionality of medical devices. For example, laser cutting is used to manufacture intricate components of stents and surgical tools, ensuring high precision and reliability. This technology also supports the production of custom and patient-specific devices, improving patient outcomes.
Custom Prosthetics
- Typical Wattage: 100-300 watts
- Applications: Cutting and engraving materials used in custom prosthetics, including polymers and composites.
- Benefits: Allows for the customization of prosthetics to meet individual patient needs, ensuring a perfect fit and comfort. This customization process is crucial for enhancing the quality of life for prosthetic users, as it ensures better functionality and comfort.
Educational Applications
Educational institutions use laser cutting technology as a teaching tool and for various academic projects. Lower wattage lasers are typically sufficient for these applications, providing a balance between functionality and safety.
Academic Projects
- Typical Wattage: 30-100 watts
- Applications: Cutting and engraving materials such as cardboard, wood, and acrylic for prototypes, models, and other educational projects.
- Benefits: Enables students to learn about laser technology and its applications while creating tangible projects that enhance their understanding. By engaging in hands-on projects, students gain practical experience with cutting-edge technology, fostering innovation and problem-solving skills.
Research and Development
- Typical Wattage: 100-300 watts
- Applications: Experimental cutting and engraving for research purposes, including material science and engineering studies.
- Benefits: Provides the flexibility to explore new materials and cutting techniques, fostering innovation and discovery. This hands-on experience is invaluable for students and researchers, allowing them to test hypotheses and develop new technologies.
VII. FAQs

1. Is higher wattage always better in laser-cutting machines?
While higher wattage machines offer advantages in speed and material versatility, they are not always the best choice for all applications. Excessive power can lead to increased thermal damage, impurities in cut quality, and higher operational costs.
Therefore, the selection should consider the material type, thickness, and the specific requirements of the cutting application. Balancing wattage with the precise needs of the task ensures efficiency without compromising quality.
2. Are there safety risks associated with higher-wattage laser cutters ?
Yes, higher wattage laser cutters pose significant safety risks due to their powerful beams, which can cause severe injuries, burns, and eye damage if not properly managed. Proper safety measures are essential:
- Operator Training: Ensure comprehensive training for all operators.
- Personal Protective Equipment (PPE): Use laser safety glasses and other protective gear.
- Machine Safety Features: Implement interlocks and emergency stop mechanisms.
- Controlled Environment: Maintain restricted access and proper ventilation.
3. Can lower-wattage laser cutters be upgraded to higher wattages?
Upgrading a laser cutter’s wattage involves significant modifications, including the installation of a more powerful laser source and potentially upgrading other machine components like power supplies and cooling systems.
Such upgrades are complex and costly, often making it more feasible to invest in a new machine better suited to higher power needs. Consultation with the manufacturer is advised to explore viable upgrade options.
suspension working platform,fibreglass working platform,aluminum working platform
Hubei Chenglongwei Special Purpose Vehicle Co., Ltd. , https://www.clw-automobile.com