3. Thermal Polymerization Drying This ink must be heated after printing to undergo polycondensation and cure. Heat curing ink is a mixture of resin and curing agent, and then printed and heated to make the resin react to form an ink film. This kind of ink is called heat polymerization ink. The advantages are one-liquid type, solvent-free, stable viscosity before heating, good fastness and resistance to printing on the printed product, and the disadvantage of high energy consumption. The curing speed of this ink depends on the content of the catalyst and the heating temperature. When no catalyst is added, the ink needs to be cured at a temperature higher than 150 degrees. After the catalyst is added, it can be cured at an intermediate temperature. However, the catalyst has a large content and does not facilitate the preservation of the ink. The physical properties of this ink's hardened ink film are very good, mainly for metal and plastic printing.
4. Colloidal drying Colloidal drying ink using plastic sol ink. The ink disperses the polyvinyl chloride together with the pigment in the plasticizer. After printing, the polyvinyl chloride particles expand under the action of the plasticizer and form a plasticized polyvinyl chloride film. Thus, the polyvinyl chloride film is realized. dry. Plastic adhesive ink can be used as foaming ink, printing and dyeing ink and fiber ink.
5. Drying by filtration The method of drying by combination of osmotic drying and gel drying is called filtration drying. When the coating is printed with a fast-drying ink, the low-viscosity petroleum solvent in the binder is quickly absorbed into the coating by capillary action of the coating. The resin components that have been expanded into a gel form contain the pigment particles therein, remain on the paper, and the ink cures.
6. Wet-Solid Drying Wet-printing ink is used to print on paper, and steam is blown in. Moisture in the air or water in the paper is absorbed by the ink. The resin dissolved in alcohol at the same time precipitated and precipitated. The ink begins to dry, and the water eventually evaporates out of the paper due to volatilization. When using this kind of ink, special attention should be paid to picking the proper ink roller.
7. Precipitation Drying Precipitated drying inks are made by dissolving high acidity resins in alcohols. The resins used must have limited solubility with water, but they will precipitate sooner than the limited amount, typically representing a change in rosin. Maleic resin. Commonly used alcohol solvents such as ethylene glycol. The drying of the ink is performed with water as a precipitant, so the solvent used for the ink must be able to mix with water in any ratio.
8. Condensation Drying Wax inks are very important cold-set inks. For example, a carbon-carbon ink is heated and printed, is a solid at normal temperature, and when printed on a voucher printing machine, it is fluidized by heating and melting, and can be printed with a relief plate or a lithographic plate, and is condensed and dried through a cooling roller.
9. Microwave Drying Microwave drying is also a means of heating the ink to dry it. Under the action of the microwave electromagnetic field, the heated media molecules become polarized molecules with positive and negative charges. These polarized molecules vibrate with the change of the electromagnetic field, and the temperature also increases.
10. Reaction Curing Type This ink is different from the previous two-component reactive curable ink. When the ink comes into contact with paper, certain components of the ink react with a certain component of the paper and dry and solidify. This reaction exists on the coating layer on the surface of the ink and paper, so that the ink cures rapidly and there is no problem of volatile pollution. However, inks and papers that can react with each other must be selected for printing.
11. Pressure solidification Pressurizes the microcapsules with pressure, causing them to break down and cause a chemical reaction. That is, the ink is made into microcapsule particles. During the printing process, the ink microcapsules are pressed and the microcapsules are broken. The two components react and rapidly/curing. This drying process is pollution-free and requires no drying device.
4. Colloidal drying Colloidal drying ink using plastic sol ink. The ink disperses the polyvinyl chloride together with the pigment in the plasticizer. After printing, the polyvinyl chloride particles expand under the action of the plasticizer and form a plasticized polyvinyl chloride film. Thus, the polyvinyl chloride film is realized. dry. Plastic adhesive ink can be used as foaming ink, printing and dyeing ink and fiber ink.
5. Drying by filtration The method of drying by combination of osmotic drying and gel drying is called filtration drying. When the coating is printed with a fast-drying ink, the low-viscosity petroleum solvent in the binder is quickly absorbed into the coating by capillary action of the coating. The resin components that have been expanded into a gel form contain the pigment particles therein, remain on the paper, and the ink cures.
6. Wet-Solid Drying Wet-printing ink is used to print on paper, and steam is blown in. Moisture in the air or water in the paper is absorbed by the ink. The resin dissolved in alcohol at the same time precipitated and precipitated. The ink begins to dry, and the water eventually evaporates out of the paper due to volatilization. When using this kind of ink, special attention should be paid to picking the proper ink roller.
7. Precipitation Drying Precipitated drying inks are made by dissolving high acidity resins in alcohols. The resins used must have limited solubility with water, but they will precipitate sooner than the limited amount, typically representing a change in rosin. Maleic resin. Commonly used alcohol solvents such as ethylene glycol. The drying of the ink is performed with water as a precipitant, so the solvent used for the ink must be able to mix with water in any ratio.
8. Condensation Drying Wax inks are very important cold-set inks. For example, a carbon-carbon ink is heated and printed, is a solid at normal temperature, and when printed on a voucher printing machine, it is fluidized by heating and melting, and can be printed with a relief plate or a lithographic plate, and is condensed and dried through a cooling roller.
9. Microwave Drying Microwave drying is also a means of heating the ink to dry it. Under the action of the microwave electromagnetic field, the heated media molecules become polarized molecules with positive and negative charges. These polarized molecules vibrate with the change of the electromagnetic field, and the temperature also increases.
10. Reaction Curing Type This ink is different from the previous two-component reactive curable ink. When the ink comes into contact with paper, certain components of the ink react with a certain component of the paper and dry and solidify. This reaction exists on the coating layer on the surface of the ink and paper, so that the ink cures rapidly and there is no problem of volatile pollution. However, inks and papers that can react with each other must be selected for printing.
11. Pressure solidification Pressurizes the microcapsules with pressure, causing them to break down and cause a chemical reaction. That is, the ink is made into microcapsule particles. During the printing process, the ink microcapsules are pressed and the microcapsules are broken. The two components react and rapidly/curing. This drying process is pollution-free and requires no drying device.
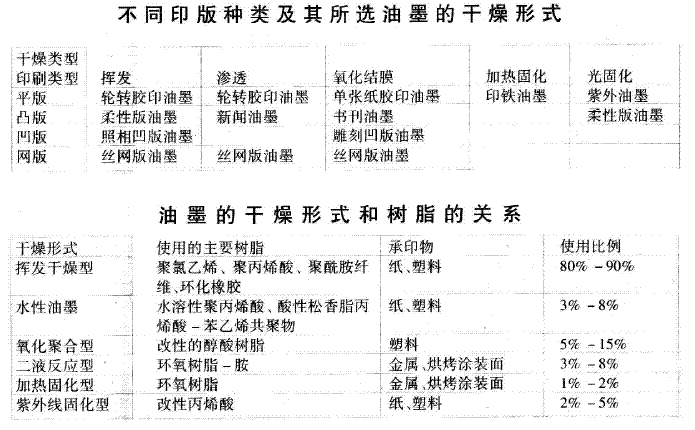