Abstract: Rejuvenating CNC machine tool industry and realizing industrialization are the only way to develop China's machinery manufacturing industry. The reliability ratio of CNC system is also a requirement of users, especially for the CNC system used in modern production lines. The market requires long-term normal operation of CNC machine tools. This first of all requires the CNC system to work reliably for a long period of time. Reliability In the research and development, design and manufacturing chain of numerical control system products, quality and level are most comprehensively reflected, including technology and management level. This article takes Japan's FANUC company as an example to illustrate that because of the company's emphasis on the reliability of CNC systems, its products are welcomed by users.
FANUC is a company specializing in the production of factory automation related products. Its main products are CNC machine tools and robots. One-third of all employees in FANUC focus on research and development work. At present, the market share of numerical control systems supporting numerical control machine tools, FANUC accounts for about 70% in Japan, accounting for about 50% in the world. How does FANUC's products get pushed by the world's machine tool industry?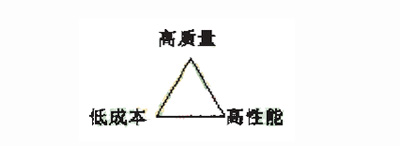
1. Product Development and Verification First of all, FANUC Corporation clearly defined the guidelines for product development as follows: (1) High performance: The system adopts the latest and most advanced technologies to meet users' requirements for high performance. (2) High quality: The first is high reliability to ensure that goods can be safely operated anywhere in the world. (3) Low cost: Users can obtain high economic benefits, so that the user's products can be competitive in the international market. As shown in Figure 1.
The purpose of using FANUC products on the production line is to achieve the best performance of the machine. In order to better meet the requirements of users, FANUC will also install similar products on its own production line equipment to maximize the use and test of these products. Products, as far as possible to play and use the technological advancement of the product to prove that the product is reliable and durable. FANUC believes that in its own factory, due to the robotization of the automated production process (ie, the production process is unmanned and basically carried out by robots), the product can be subjected to high-strength tests. For example, FANUC's new servo motor factory has only 43 employees. The operator, 288 robots, and an automated warehouse use FANUC's own control system. In this factory, the ratio of the operator to the robot is 1:6.7 for all processes from the transport, assembly, testing, packaging and delivery of motor parts. FANUC's own control system, CELL60, is used in FANUC's heavy-duty machine shop, which can operate for 72 hours, including Saturday and Sunday. In all FANUC factories, there are now 430 operators and 922 robots. The ratio of operators to robots is 1:2.1. All these robotized factories are produced in compliance with ISO9001 international standards. In order to ensure that the FANUC Commodity Headquarters is used in the best condition on the user's production line, FANUC provides a worldwide maintenance and service network. These services include on-site installation, commissioning, testing, periodic maintenance, fault diagnosis and repair, and maintenance. spare parts. In this way, as long as the user's production line is working, it can provide services for FANUC products. FANUC's maintenance service support system, called CS24, is connected to the communications network through computers. The detailed service records provided by this system have a great effect on improving the reliability of the system.
2. The goal of high-reliability design When FANUC develops products, its project leader is responsible for the commercialization of the product: satisfying the needs of the user and putting forward production. Clean performance grade planning, evaluation and selection of components to achieve high reliability and achieve cost and manufacturing goals. From the needs of the market to everything in the manufacturing system, the person in charge of project development must be familiar with the design and manufacture of high quality and high reliability products.
Needless to say, reliability design is very important in product development. FANUC strictly follows the design standardization regulations and formulates as many design and production standards as possible. For the selection of components, it is necessary to verify their reliability, such as heat and vibration characteristics, in order to conduct a thorough evaluation of them. In addition, FANUC proposed "Reducing the Number of Parts" as a design goal for each product to ensure product reliability. At the entrance to the FANUC Institute. Hanging a slogan "WenigerTeile" is asking developers to use the "fewer parts" concept when designing goods. It also stated that reducing the number of components can also increase productivity, reduce costs, and reduce maintenance.
For product development, FANUC uses the product's failure rate as a quantitative goal of reliability. For example, the target system failure rate of the CNC system, including the motor and servo system, is 0.01 times per month, which represents an average of 0.1 failures per month per CNC, that is, 1 failure per 100 months. In order to more clearly define the company’s responsibility for the product, FANUC has developed and manufactured its own major spare parts, such as printed circuit boards and servo motors. Although FANUC's dedicated chips are manufactured by specialized manufacturers, FANUC is also designed within the company to ensure performance and reliability. This is how FANUC manages reliability.
3. High-Reliability Design Points The environment, CNC system, FA-related products, and robot design must first consider the environment. Through continuous reliable operation, the product is exposed to harsh environments such as temperature, humidity, vibration, and contamination. The safe use of oil mist is very important. When designing products, it is important to evaluate the reliability of the product and the product itself.
For FANUC, the main reliability assessment programs are resistance to heat, cold, humidity, vibration, durability, noise, dust, cutting oil, and static electricity, as well as evaluation of the electronic components' materials and structures tolerant to high temperature cutting oil impregnation. The ability to confirm the effect of corrosion on components exposed to cutting oils during processing and to evaluate most commonly used cutting oils.
Minimizing FANUC products is moving toward the miniaturization process of CNC, and it also pays full attention to reliability issues in miniaturization.
Reducing the lead distance of the electronic components Generally, the lead distance of the IC is 2.54 mm, which has been reduced to 0.5 mm or less. The small distance between the conductive wires may cause the leakage of the current through the capacitor in a severe environment and cause the failure of the CNC system. Therefore, applying a coating made of some insulating material on the printed board can avoid this failure.
When printed circuit boards use micro circuit components, some measures have also been taken to ensure reliability.
Choose the best materials that are resistant to moisture and cutting oils.
Choose the best die bond area to ensure adequate weld strength and weld productivity.
For large-size surface mount components, the coefficient of expansion of the printed board material should be selected as close as possible to the coefficient of expansion of the components to prevent deterioration of the quality of the solder joint due to the difference in the coefficient of expansion.
Since the failure rate of electronic components increases with increasing temperature, in order to reduce the amount of heat generated due to high-density mounting and maintain a low temperature rise, a temperature is set around the components and the semiconductor junction temperature during operation. Allowed upper limit to reduce heat loss.
In order to prevent contactor miniaturization and multiple lead-induced electrical failures, such as reduced contact pressure on the surface and contact failure due to foreign matter on the contact surface, 2-point contact is used to ensure that the contact surface is clean.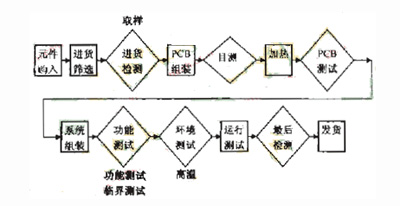
4. High-reliability manufacturing In product development, the responsible person must consider the entire manufacturing process in designing, and must ensure quality. Stable manufacturing and reliability are ensured by robots and automated equipment. FANUC pays great attention to the reliability of the manufacturing process and eliminates defective products by testing the aging and performance of components. In this way, early failures and failures in the operation will not occur on the user's equipment. For example, during the inspection of germanium devices, the components are subjected to aging at high temperatures; the printed boards are aged at a high temperature before the performance test; and the assembled CNC is subjected to a high temperature operation test, and all the mechanical units, such as robots, are manufactured before shipment. 100h running test etc. All test and aging records are stored in a reliable database. Using this data, it plays a significant role in improving the reliability of FANUC products. Figure 2 shows the manufacturing process of the CNC.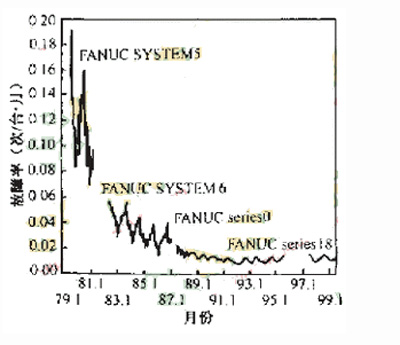
5, high reliability of maintenance and reliability related work maintenance database FANUC attaches great importance to service and maintenance. It stores the detailed services and supporting tasks provided to users in chronological order in the maintenance database. The FANUC stores the relevant fault conditions that occur on the user's device, the total number of which is about the blade, such as the user's name, the date the phone was received, the date of the repair, the name of the module, the serial number, the specification of the faulty unit, the contents of the repair, the fault's Causes and so on. All the fault information stored in this database has become the data source for the user to query the fault history. The information of these projects was also used to count monthly changes in the failure rate of devices, units, and components to improve and enhance the reliability of development and manufacturing departments and repair parts. It was also used by FANUC for quality management.
Reliability prediction The above database is also used for high reliability design, for example, predicting the reliability of new products.
ISO9000 certification FANUC has obtained ISO9002 certification in June 1993 and ISO9001 certification in July 1997.
FANUC System Reliability Progress The failure rate of FANUC products is shown in Figure 3. As can be seen from the figure, the reliability of FANUC products has increased year by year.
FANUC is a company specializing in the production of factory automation related products. Its main products are CNC machine tools and robots. One-third of all employees in FANUC focus on research and development work. At present, the market share of numerical control systems supporting numerical control machine tools, FANUC accounts for about 70% in Japan, accounting for about 50% in the world. How does FANUC's products get pushed by the world's machine tool industry?
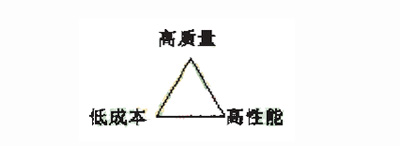
Figure 1 FANUC Development Policy
1. Product Development and Verification First of all, FANUC Corporation clearly defined the guidelines for product development as follows: (1) High performance: The system adopts the latest and most advanced technologies to meet users' requirements for high performance. (2) High quality: The first is high reliability to ensure that goods can be safely operated anywhere in the world. (3) Low cost: Users can obtain high economic benefits, so that the user's products can be competitive in the international market. As shown in Figure 1.
The purpose of using FANUC products on the production line is to achieve the best performance of the machine. In order to better meet the requirements of users, FANUC will also install similar products on its own production line equipment to maximize the use and test of these products. Products, as far as possible to play and use the technological advancement of the product to prove that the product is reliable and durable. FANUC believes that in its own factory, due to the robotization of the automated production process (ie, the production process is unmanned and basically carried out by robots), the product can be subjected to high-strength tests. For example, FANUC's new servo motor factory has only 43 employees. The operator, 288 robots, and an automated warehouse use FANUC's own control system. In this factory, the ratio of the operator to the robot is 1:6.7 for all processes from the transport, assembly, testing, packaging and delivery of motor parts. FANUC's own control system, CELL60, is used in FANUC's heavy-duty machine shop, which can operate for 72 hours, including Saturday and Sunday. In all FANUC factories, there are now 430 operators and 922 robots. The ratio of operators to robots is 1:2.1. All these robotized factories are produced in compliance with ISO9001 international standards. In order to ensure that the FANUC Commodity Headquarters is used in the best condition on the user's production line, FANUC provides a worldwide maintenance and service network. These services include on-site installation, commissioning, testing, periodic maintenance, fault diagnosis and repair, and maintenance. spare parts. In this way, as long as the user's production line is working, it can provide services for FANUC products. FANUC's maintenance service support system, called CS24, is connected to the communications network through computers. The detailed service records provided by this system have a great effect on improving the reliability of the system.
2. The goal of high-reliability design When FANUC develops products, its project leader is responsible for the commercialization of the product: satisfying the needs of the user and putting forward production. Clean performance grade planning, evaluation and selection of components to achieve high reliability and achieve cost and manufacturing goals. From the needs of the market to everything in the manufacturing system, the person in charge of project development must be familiar with the design and manufacture of high quality and high reliability products.
Needless to say, reliability design is very important in product development. FANUC strictly follows the design standardization regulations and formulates as many design and production standards as possible. For the selection of components, it is necessary to verify their reliability, such as heat and vibration characteristics, in order to conduct a thorough evaluation of them. In addition, FANUC proposed "Reducing the Number of Parts" as a design goal for each product to ensure product reliability. At the entrance to the FANUC Institute. Hanging a slogan "WenigerTeile" is asking developers to use the "fewer parts" concept when designing goods. It also stated that reducing the number of components can also increase productivity, reduce costs, and reduce maintenance.
For product development, FANUC uses the product's failure rate as a quantitative goal of reliability. For example, the target system failure rate of the CNC system, including the motor and servo system, is 0.01 times per month, which represents an average of 0.1 failures per month per CNC, that is, 1 failure per 100 months. In order to more clearly define the company’s responsibility for the product, FANUC has developed and manufactured its own major spare parts, such as printed circuit boards and servo motors. Although FANUC's dedicated chips are manufactured by specialized manufacturers, FANUC is also designed within the company to ensure performance and reliability. This is how FANUC manages reliability.
3. High-Reliability Design Points The environment, CNC system, FA-related products, and robot design must first consider the environment. Through continuous reliable operation, the product is exposed to harsh environments such as temperature, humidity, vibration, and contamination. The safe use of oil mist is very important. When designing products, it is important to evaluate the reliability of the product and the product itself.
For FANUC, the main reliability assessment programs are resistance to heat, cold, humidity, vibration, durability, noise, dust, cutting oil, and static electricity, as well as evaluation of the electronic components' materials and structures tolerant to high temperature cutting oil impregnation. The ability to confirm the effect of corrosion on components exposed to cutting oils during processing and to evaluate most commonly used cutting oils.
Minimizing FANUC products is moving toward the miniaturization process of CNC, and it also pays full attention to reliability issues in miniaturization.
Reducing the lead distance of the electronic components Generally, the lead distance of the IC is 2.54 mm, which has been reduced to 0.5 mm or less. The small distance between the conductive wires may cause the leakage of the current through the capacitor in a severe environment and cause the failure of the CNC system. Therefore, applying a coating made of some insulating material on the printed board can avoid this failure.
When printed circuit boards use micro circuit components, some measures have also been taken to ensure reliability.
Choose the best materials that are resistant to moisture and cutting oils.
Choose the best die bond area to ensure adequate weld strength and weld productivity.
For large-size surface mount components, the coefficient of expansion of the printed board material should be selected as close as possible to the coefficient of expansion of the components to prevent deterioration of the quality of the solder joint due to the difference in the coefficient of expansion.
Since the failure rate of electronic components increases with increasing temperature, in order to reduce the amount of heat generated due to high-density mounting and maintain a low temperature rise, a temperature is set around the components and the semiconductor junction temperature during operation. Allowed upper limit to reduce heat loss.
In order to prevent contactor miniaturization and multiple lead-induced electrical failures, such as reduced contact pressure on the surface and contact failure due to foreign matter on the contact surface, 2-point contact is used to ensure that the contact surface is clean.
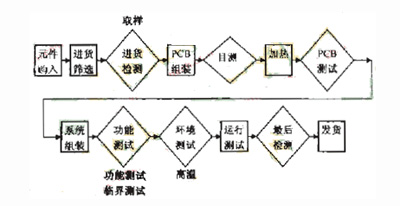
Figure 2 FANUCCNC controller manufacturing process
4. High-reliability manufacturing In product development, the responsible person must consider the entire manufacturing process in designing, and must ensure quality. Stable manufacturing and reliability are ensured by robots and automated equipment. FANUC pays great attention to the reliability of the manufacturing process and eliminates defective products by testing the aging and performance of components. In this way, early failures and failures in the operation will not occur on the user's equipment. For example, during the inspection of germanium devices, the components are subjected to aging at high temperatures; the printed boards are aged at a high temperature before the performance test; and the assembled CNC is subjected to a high temperature operation test, and all the mechanical units, such as robots, are manufactured before shipment. 100h running test etc. All test and aging records are stored in a reliable database. Using this data, it plays a significant role in improving the reliability of FANUC products. Figure 2 shows the manufacturing process of the CNC.
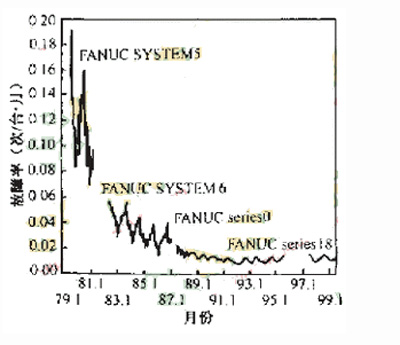
Figure 3 FANUC system failure rate
5, high reliability of maintenance and reliability related work maintenance database FANUC attaches great importance to service and maintenance. It stores the detailed services and supporting tasks provided to users in chronological order in the maintenance database. The FANUC stores the relevant fault conditions that occur on the user's device, the total number of which is about the blade, such as the user's name, the date the phone was received, the date of the repair, the name of the module, the serial number, the specification of the faulty unit, the contents of the repair, the fault's Causes and so on. All the fault information stored in this database has become the data source for the user to query the fault history. The information of these projects was also used to count monthly changes in the failure rate of devices, units, and components to improve and enhance the reliability of development and manufacturing departments and repair parts. It was also used by FANUC for quality management.
Reliability prediction The above database is also used for high reliability design, for example, predicting the reliability of new products.
ISO9000 certification FANUC has obtained ISO9002 certification in June 1993 and ISO9001 certification in July 1997.
FANUC System Reliability Progress The failure rate of FANUC products is shown in Figure 3. As can be seen from the figure, the reliability of FANUC products has increased year by year.
China Tire Seal,Safety Seal Tire Plugs,Tyre Sealant,Slime Inner Tube, we offered that you can trust. Welcome to do business with us.
Tire Seal,Safety Seal Tire Plugs,Tyre Sealant,Slime Inner Tube
KRONYO United Co., Ltd. , https://www.taibeikronyo.com