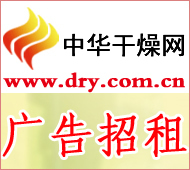
China Drying News reported on the 3rd from Huaibei Zhongrun Bio-energy Technology Development Co., Ltd. that the company's successfully developed cellulosic biomass simultaneous hydrolysis technology was completed at the end of 2012 after acceptance of the “863†results of the Ministry of Science and Technology in September 2012. Pilot tests, and plans to start industrialization work in 2013. This indicates that China has taken the lead in the world to make a breakthrough in the third generation of biomass refining technology, which is several decades ahead of time predicted by foreign scientists to convert all plant components into oil substitute products. The success of this technology means that the biomass refining technology has entered the third generation stage.
Huaibei Zhongrun lasted nearly 7 years, invested nearly 200 million yuan successfully developed cellulosic biomass simultaneous hydrolysis technology, can simultaneously convert all the organic components of the plant into small molecular organic matter. This technology is not only the first to achieve a complete hydrolysis of lignin in the world, at the same time, the reaction has a high selectivity. There are only two organics in the simultaneous hydrolysis product: small molecular aromatics and small organic acids.
Small molecular aromatics are widely used and have large amounts, such as toluene, p-xylene, mesitylene, mesitylene, etc. Currently, they basically come from petroleum.
The small molecule organic acid products obtained by simultaneous hydrolysis are mainly lactic acid, supplemented by glycolic acid and formic acid, and a small amount of other organic acids. Lactic acid and glycolic acid are the main monomers for the preparation of biodegradable plastics. Formic acid is the carrier of hydrogen. The “863†acceptance results show that 1 ton of plants can be hydrolyzed to obtain 1 ton of organic matter, in which the production of small molecule aromatics exceeds 20%, the highest can exceed 30%, the yield of lactic acid is approximately 35%, and the amount of glycolic acid is approximately 10%. About 10%.
The use of plants as raw materials for the production of toluene products, compared with the production process of the petrochemical refining process, Huaibei Zhongrun simultaneous hydrolysis refining technology production process steps less. That is, when both are optimized, the production cost of the toluene product of the plant material is expected to be lower than the petrochemical route.
The current global plant-refining technology is in the pilot stage of the first-generation technology industrialization and second-generation technology R&D. The first generation of technology uses edible sugars, starches, animal and vegetable fats and oils as raw materials, and prepares chemicals or liquid fuels. Its biggest drawback is competing with people for food. The second generation technology uses plants as raw materials, and its main disadvantage is that the products are single. The organic yield is very low. In essence, generation 1 and 2 technologies do not have the ability to compete in the market and require the support of governments of all countries.
In 2006, international scientists speculated that a third-generation technology will emerge in a few decades. That is, all plant components will be converted into products without the need for component separation. Similar to petrochemical refining production processes, polymers in plants are solved at the lowest cost. Gathered into small molecular organics, and the selectivity of the target product is high, liquid transportation fuels and chemical products can be prepared at the same time, and the new process can be integrated into the existing petrochemical refining production process. Today, this speculation is realized in advance by Huaibei Zhongrun Bio-energy Technology Development Co., Ltd.
Frame Wiper Blade,Conventional Wiper Blae,Frame Wiper Blade
Multi-Functional Wiper Blade Co., Ltd. , http://www.nscarhorn.com