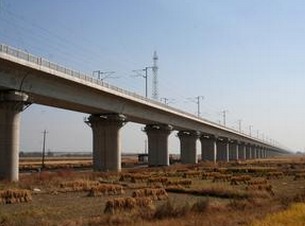
The demand for machine tools in the rail transit industry can be roughly divided into four aspects: first, rail processing and high-speed railway pillow processing; second, the manufacture of locomotives and vehicles; thirdly, the manufacture of wheels and vehicle parts; and fourth, the operation of machine tools in the rail transit industry. Daily maintenance. These four areas cover almost all rail transit industry chains, including road network construction, vehicle manufacturing, operation and maintenance, etc. The amount of the rail transit industry's annual purchase of machine tools is close to 7 billion yuan. Obviously, the rail transit industry has become a very important emerging customer base in the Chinese machine tool market.
Is it luck or strength?
Many key products of rail transit have very high rigidity, stability, and precision requirements for processing equipment. This virtually sets a high threshold for companies that want to enter this market. However, we can still be pleasantly surprised to see that even in such harsh conditions, there are still some machine tool companies that rely on their own leading product technology, highly effective customized solutions, and high-quality pre-sales service. Rail transit market.
Here we select some representative companies to explore how they did it through their success in the rail transit market.
DMG: The machine tool was successfully applied to the Dageki Group, a well-known German machine tool company, on the Zhiqi Railway. It closely follows the market and has been fully prepared for the rail transportation, energy and other industries that the Chinese government has vigorously supported. According to reports, the DMU 125 FD duo BLOCK and DMC 125 FD duo BLOCK of the DMG Group's milling and compounding center have been successfully applied to the machining of the wheels of the trains of Zhiqi Railway Equipment Co., Ltd.
Zhiqi Railway Equipment Co., Ltd. possesses wheel processing lines, axle processing lines, wheelset assembly lines, and wheelset inspection lines. It is a professional international manufacturer of high-speed railway EMU wheelsets. Its products cover the China High Speed ​​Rail Harmony Group wheelsets with speeds of 200 to 380 kilometers per hour and pairs of speeds of 400 to 500 kilometers per hour for super high-speed test trains.
DMG 125 FD duoBLOCK Milling Compound Center DMG Group
At present, Zhiqi has six DMC milling and milling centers DMC125FDduoBLOCK and one DMU125FDduoBLOCK. As a production line proficient in wheelset processing, whether it is a large tool or mold manufacturing, mechanical, automotive, model, instrument manufacturing, or in the aerospace industry, as long as the large batch processing workpiece, DMU / CFD type milling compound Machining centers will show their talents. The gantry structure, which is most suitable for machining large workpieces, is used as the machine tool design. It embodies the rigidity of the machine structure to the greatest extent. At the same time, the thermal symmetry structure has a liquid-cooled ball screw drive mechanism and a cooling feed motor in all axes. Guaranteed long-term accuracy.
The application of the DMG machine tool in the processing of the Zhiqi EMU wheels enables the complete machining of turning, drilling, boring and tilting oil holes in a single clamping. The design of the double exchange table is such that the auxiliary clamping time of the workpiece is almost zero.
Danobart: Providing a comprehensive solution for high-speed rail systems
As one of the most powerful industrial groups in the European continent, the Danobart Group has also set up an engineering technology company for the railway industry. It specializes in the development and production of advanced vertical lathes and is suitable for high-efficiency machining of heavy-duty railway wheels.
Danobart said that so far, customers have different suppliers in the industry, so that customers have to mix and use different technologies, different after-sales services, different professional knowledge and skills, different ways of doing things, and even Use different languages. Danobart Railway Systems, on the other hand, is committed to providing users with total solutions that meet all aspects of their needs.
For the design of train axles, Danobart uses the latest developments in machinery and production systems to achieve higher precision and longer product life. In addition, with a complete manufacturing solution, the automatic feeding equipment is applied at the same time to avoid non-precision and personnel interference, ensuring the correct tracking of the parts in the entire workshop and reducing the cost of the wheel set. Automated production systems provide users with a truly complete processing technology. Moreover, multiple uses can be realized to improve the user's production. The tracking of parts can be controlled at every moment. At the same time, the production line can also provide a real-time report on why the parts were rejected by the system.
MKB7025 type CNC track board
The specialization of different markets has enabled Danobart Group to develop a new strategy and focus on the positioning of different markets. This is why the Danobart Group categorizes its products and provides users with complete solutions and single equipment.
In terms of services, Danobart Group Railway System Company tells us that their goal is not only to provide equipment, but also to become a user's technology partner, to provide users with engineering services, service throughout the entire planning and assembly process, and the subsequent use of the product.
Looking at its range of operations, Danobart Group offers all machining operations ranging from the cutting of steel shavings to the balancing of wheelsets as well as non-destructive testing and automatic loading systems. In addition, wheel-pair renovations are provided without having to disassemble the wheelsets from the train. In addition to the wheelset solution, Danobant Railway Systems has also developed a special solution for the machining of cast iron bogies (for 3-piece construction of trucks), that is, through a rotating device (B-axis) and dedicated on high-speed horizontal machining centers. Machine tool fixtures for processing.
It is well known that the complexity of part shapes (braces and bezels) makes saving time the most basic requirement and that all solutions will be based on high productivity needs. Compared to competitors, Danobart offers solutions with a short time (in the up/down process) and high machining accuracy. Perhaps this is precisely why the giant machine tool industry has been invincible in the rail transit market for many years.
Hangzhou Machine Tool: A Major Role in High-speed Rail Construction
Looking back to the Chinese home market. Compared with a multinational machine tool group with world-class technology and complete solutions, most Chinese machine tool companies cannot compete with each other in their market competitiveness. Hangzhou Machine Tool Group Co., Ltd. is an exception.
In 2010, the 160-kilometer-long Shanghai-Hangzhou high-speed railway with a design speed of 350 kilometers per hour was officially opened. The MKB7025 CNC track plate special grinder for service on the super high-speed railway line Jiashan Board is being developed by Hangzhou Machine Tool Group Co., Ltd.
In order to improve the stability and durability of the track under high-speed operating conditions, reduce the late-track maintenance, and effectively reduce the overall cost, it is necessary to change the structural form of the track-based foundation and put forward high-precision, high-stability, and Less maintenance requirements. Therefore, the adoption of ballastless track structures is the direction of development of high-speed railways at home and abroad, and it is an integrated application of contemporary high-tech.
The track plate replaces the previous sleeper, through mixing and proportioning of the cement prefabricated, and after being precisely processed by a special CNC track plate grinding machine, it is laid on the whole road section, and the rail is fixed on the track plate subgrade, meeting the train's 350 kilometers per hour high speed and safe driving needs. .
The Hangji Group spotted a rare historical opportunity for the country to expand domestic demand to invest in and build high-speed railways. With nearly half a century of grinding machine technology experience and brand awareness, the company has entered the country’s booming high-speed railway industry and has successively undertaken 14 special projects. Grinding of the development task of grinding machine for the MKB7025 CNC track plate for CRTSII type track plates.
To process 6.5 meters long, 2.55 meters wide, 1.2 meters high, weighing 9 tons of high-speed railway track slabs, track plate grinding machine can be called a giant, Hangzhou machine's MKB7025 CNC track plate grinding machine length 12.8 meters, With a width of 7.5 meters and a height of 5.5 meters, the beam components of the machine grinding head weigh 45 tons and a single machine tool weighs 130 tons.
This series of products has obtained three patented technologies granted by the National Patent Office: "Girder Moving CNC Grinding Machine" with gantry frame-type overall movement method; "High-speed locking mechanism of grinding head rotary shaft" "The device" adopts advanced hydraulic automatic load-bearing, automatic leveling and stress-free clamping technology for the heavy-duty workpiece of 9 tons, such as "large-scale workpiece hydraulic support leveling and clamping device".
The product's innovation is also manifested in the use of double gear electronic anti-backlash structure to ensure the accuracy of the transmission of the main feed axis; machine automation, automatic generation of processing programs, automatic grinding, feeding, positioning, leveling, clamping, automatic Measure and judge pass or fail, automatically record data, and engrave track plate ID number.
After the MKB7025 CNC track plate grinding machine prototype was installed and used, it passed the “certified certification†of the Ministry of Railways after being verified by production certification, and after using the Shanghai-Hangzhou Railway Line, the Hangzhou-Ningbo Railway Line, and the Hangzhou-Nanjing Railway Line Plate, it was thought The machine tool can replace similar imported processing equipment, and its main precision and performance have reached the level of international similar products.
Cable Box,Cable Terminal Box,Cable Clamp,Elevator Component,Single Cable Box
Fenghua Jade Motor Co., Ltd. , http://www.chinaevatorparts.com